Universal By Name But Not Necessarily By Nature
28/11/17
Cashflow and cost of materials are always the priority of any plastics processor. So, it is not uncommon for injection moulders to adopt universal masterbatches as a convenient option. Generally, they are considered to be a quick and effective colouring solution. However, when you compare their performance during processing and the aesthetics of the finished product, this is evidently a misconception and the reason why polymer-specific masterbatches are overwhelmingly preferred.
Universal masterbatches are widely available across the globe, albeit in a limited range of colours. They offer a carrier system that is generally compatible with a broad range of polymers. However, this “general compatibility” becomes questionable at high concentrations and where colour is critical. In the case of multi-component products i.e. finished products made up using two or more polymers, differences in colours are common. When assessing the colour of the various plastics used to make the product, the results are clearly lacking. It is nigh on impossible to achieve the same colour in different coloured base polymers using a universal masterbatch.
A useful analogy to illustrate this colour variation, is to compare blackcurrant cordial when it is added to water and then milk. If you were to dilute 10ml of blackcurrant cordial with 60ml of water, you would get a full bodied, burgundy coloured liquid. Pour the same volume into 60ml of milk and the result would resemble a strawberry milkshake. The exact same thing happens when you add the same universal masterbatch to crystal polystyrene and ABS. At high concentrations, which is the way to mask an underlying base colour,you can also experience a deterioration of physical properties. The finished product application and manufacturing methodshould drive the choice of colourant. Whatever the application you must consider its performance in the field and decide on the most appropriate carrier. The closer the carrier is to the moulding polymer, then the higher the probability of success.
A polymer-specific masterbatch will allow good processing and colour accuracy, without negatively affecting performance. For example, if your product is required to withstand the damaging effects of the sun’s rays, an additive can be easily added to the polymer-specific masterbatch’s unique formulation.
Many processors argue that universal masterbatches are readily available and can be accessed in smaller quantities. However, if a polymer-specific masterbatch producer operates an agile production facility, the same is also true. Universals offer a limited colour range whereas the entire spectrumof 20 million colours can be readily accessed through producers of polymer-specific masterbatches.
Performance and aesthetic qualities are paramount for any brand. Any injection moulder wanting to deliver the best – or at least a satisfactory – solution for its customers should explore the many benefits of polymer-specific masterbatch. As a compatible polymer is used to encapsulate the pigments and additives, the risk of delamination is eliminated, multi-component products can achieve the same colour,opacity and intensity, as well as maintaining inherent physical properties.
Universals, by their nature, are limited by what they are able to achieve. Due to their ability to deliver a consistent and tailored solution, polymer-specific masterbatches offer better long-term value and performance.
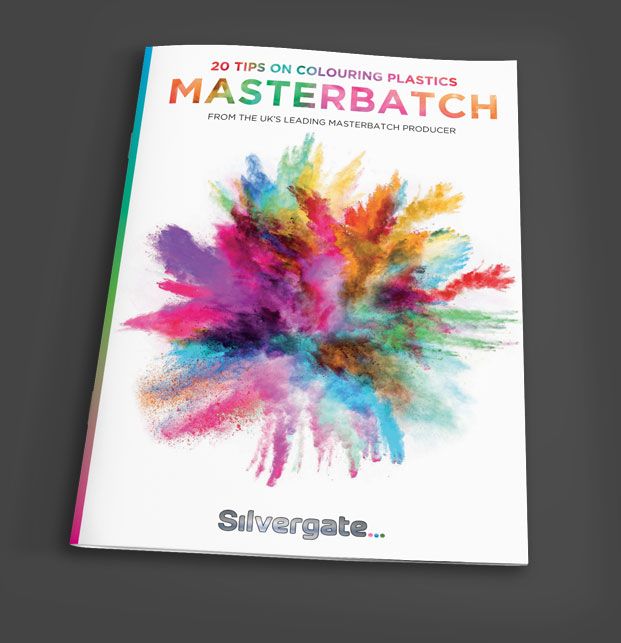
More free stuff!
Receive your Free Guide to Colouring Plastics when you sign up for our newsletter! We will only ever send exciting news that you’ll want to read, so what are you waiting for?
Sign me up to be the first to read about Silvergate’s product launches, innovations and news! We will never share your information with third parties.